Professional Packaging Machine Repair Service to Keep Your Equipment Running Efficiently
Professional Packaging Machine Repair Service to Keep Your Equipment Running Efficiently
Blog Article
Comprehending the Trick Components and Repair Service Techniques for Packaging Machine Upkeep
Reliable maintenance of packaging makers rests on a comprehensive understanding of their crucial elements, consisting of the frame, drive system, and securing devices. Recognizing common maintenance issues, combined with the application of preventative approaches and fixing techniques, can dramatically enhance device dependability. The option of repair techniques, consisting of the usage of OEM parts and the relevance of licensed specialists, plays a vital function in reducing downtime. To really comprehend the intricacies of these systems and their upkeep, one have to take into consideration the wider implications of disregarding these important practices.
Trick Components of Product Packaging Machines
Product packaging makers include several crucial parts that collaborate to make sure effective and effective packaging procedures. At the core of these devices is the frame, which provides structural stability and houses the numerous operating components. The drive system, typically a combination of gears and electric motors, assists in the activity of components, making it possible for accurate procedure throughout the product packaging cycle.
An additional crucial component is the conveyor system, which transfers products with various stages of the product packaging process. This is often enhanced by sensing units and controls that keep track of the position and rate of products, making sure synchronization and reducing mistakes. The filling system is vital for properly dispensing the best quantity of item into plans, whether in liquid, powder, or strong form.
Sealing devices, including warmth sealers or adhesive applicators, play an essential function in protecting bundles, preventing contamination and prolonging rack life. Additionally, classifying systems are important for supplying necessary product information, ensuring conformity with guidelines. Ultimately, the control board, geared up with easy to use user interfaces, enables operators to take care of maker features, monitor performance, and make changes as needed, guaranteeing optimum efficiency and effectiveness in packaging operations.
Common Maintenance Problems
Effective operation of packaging devices relies greatly on normal upkeep to avoid typical issues that can interrupt manufacturing. Amongst these issues, mechanical wear and tear prevails, particularly in elements like electric motors, conveyors, and seals, which can cause unexpected downtimes. Furthermore, imbalance of components can lead to ineffective procedure, causing products to be improperly packaged or harmed during the process.
One more usual maintenance issue includes the accumulation of dirt and debris, which can disrupt the maker's sensing units and moving components. packaging machine repair service. This not just affects efficiency however can also position safety risks. Lubrication failings can lead to increased rubbing, resulting in overheating and eventual component failure.
Electrical problems, commonly coming from loosened links or damaged circuitry, can interrupt equipment features, leading to significant production hold-ups. Software program problems due to obsolete programs or inappropriate arrangements can impede the equipment's operation, requiring immediate intervention. Dealing with these common upkeep issues proactively is vital for guaranteeing ideal efficiency and longevity of packaging equipment.
Preventative Maintenance Approaches
Executing preventative maintenance strategies is vital for sustaining the performance and reliability of packaging makers. These approaches incorporate a systematic method to maintenance, concentrating on the routine evaluation and maintenance of devices to preempt potential failures. By sticking to an arranged maintenance program, drivers can identify deterioration on elements before they cause significant break downs.
Secret elements of a preventative maintenance strategy include regular examinations, cleansing, lubrication, and element replacements based upon maker suggestions. Utilizing checklists can improve this procedure, making sure that no vital tasks are ignored. Furthermore, keeping precise records of upkeep tasks help in tracking the machine's efficiency over time, assisting in educated decision-making concerning future upkeep demands.
Training personnel on the significance of preventative upkeep enhances compliance and cultivates a culture of proactive care. Carrying out an anticipating maintenance part, using data analytics and sensor innovation, can these details better enhance machinery efficiency by anticipating failures prior to they occur.
Fixing Techniques
When confronted with malfunctions or inefficiencies in packaging equipments, using methodical troubleshooting techniques is crucial for recognizing and solving problems swiftly. The first action in effective troubleshooting is to develop a clear understanding of the equipment's functional parameters and performance metrics. This includes reviewing the machine's specifications, along with any mistake signals or codes presented.
Next, operators must perform an aesthetic inspection, inspecting for evident indicators of wear, imbalance, or damages. This usually includes analyzing belts, sensing units, and equipments to identify potential sources of breakdown. Gathering functional information, such as production prices and downtime logs, can also supply insights into recurring concerns.
When possible problems are determined, using a rational method to separate the origin is critical. This might need testing individual parts or systems in a controlled way. Participating in conversations with operators that communicate with the machinery consistently can yield important feedback regarding uncommon actions or patterns.
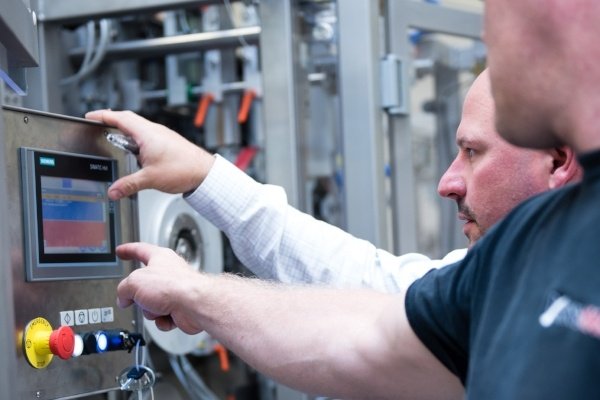
Repair Service and Substitute Finest Practices
A comprehensive understanding of repair service and substitute best practices is vital for keeping the longevity and performance of product packaging devices. Regularly evaluating the condition of device parts permits prompt intervention, protecting against more substantial problems that can bring about costly downtimes.
When repair services are required, it is vital to use OEM (Original Equipment Maker) components to ensure compatibility and performance. This not only maintains the honesty of the machine however additionally supports service warranty arrangements. Additionally, it is advisable to preserve a supply of important spare parts to facilitate quick substitutes and reduce functional disturbances.
For complex repairs, engaging licensed professionals with specialized training in product packaging equipment is advised. They have the competence to diagnose issues accurately and carry out repair work efficiently. Recording all fixing tasks and parts substitutes is important for keeping a detailed upkeep history, which can help in future troubleshooting.
Lastly, implementing a proactive method, consisting of normal evaluations and predictive maintenance methods, improves the reliability of product packaging makers. By sticking to these ideal look at this web-site techniques, businesses can ensure ideal machine performance, minimize functional risks, and prolong tools life expectancy.
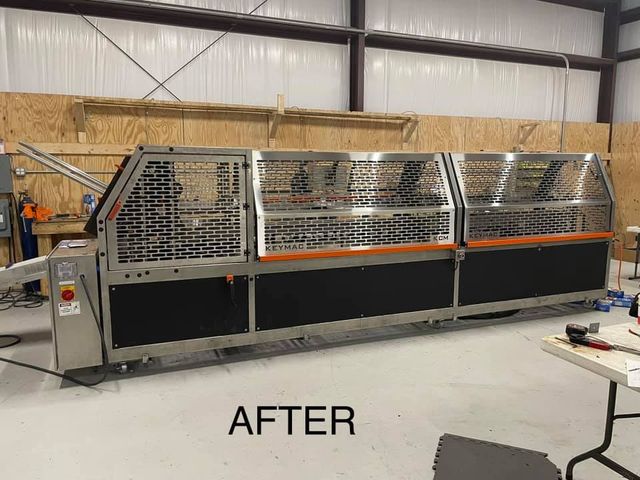
Conclusion
In final thought, a comprehensive understanding of product packaging device elements and efficient upkeep approaches is essential for optimal performance. Normal evaluations and the use of OEM components can substantially reduce downtime, while a well-documented upkeep history cultivates aggressive care. Employing qualified specialists additionally boosts fixing high quality and reliability. By executing these techniques, companies can guarantee the durability and performance of packaging devices, eventually adding to enhanced operational productivity and lowered expenses.
Effective upkeep of product packaging makers hinges on a comprehensive understanding of their essential parts, including the structure, drive system, and securing devices.Reliable operation of packaging makers depends heavily on routine maintenance to protect against common problems that can disrupt manufacturing.Carrying out preventative upkeep methods is important for maintaining the efficiency and dependability of product packaging makers. Additionally, preserving exact records of upkeep tasks help in tracking the maker's performance over time, facilitating notified decision-making pertaining to future maintenance needs.

Report this page